|
645 & 710 Over Bar Micrometers |
Over Bar Micrometers allow your line boring technician to accurately measure the diameter of EMD main bearing bores while the boring bar is in the crankcase. These Micrometers are utilized during inspection and while machining. Precision machined from aircraft aluminum, these anodized Micrometers will increase the speed and accuracy of the process while providing years of service. |
|
|
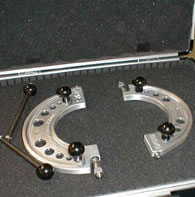 |
|
Clamp On Boring Head |
These boring heads are precision machined with a black oxide finish to create a boring head that will last for years. Each boring head consists of a hinge and clamp mechanism allowing the operator to quickly install and remove the boring head with a ¼ turn of the ratchet. Graduated in increments of .001”, a full turn of the dial creates a .050” travel on the diameter of the cut. Replaceable carbide tooling is standard off the shelf and one insert will last for several crankcases. A heavy duty design and quality construction creates a boring head that will break through a well and repeat within .001” with each application. |
|
|
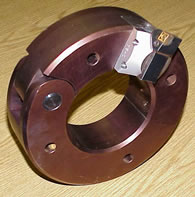 |
|
SB1000 Thrust Face Cutting Package |
The Thrust Facing Package easily connects to all of our Boring Machines enabling the operator to cut the thrust bearing surface on all EMD Crankcases. Our patented Thrust Face Bearing provides 1” of travel in graduated increments. The Thrust Facing head translates across the surface providing a smooth and accurate finish. Carbide tooling enables surface speeds up to 500 SFPM. The hardened and chromed shaft telescopes to fit all EMD Crankcases. Thrust face surfacing is a process that traditionally could only be completed on a large boring mill. Now, AEI provides the most efficient and accurate Thrust Facing Package to fit your boring machine. |
|
|
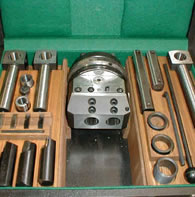 |
|
Precision Indicating Head |
Precision Indicating Heads save time by allowing the operator to locate the boring bar without the use of an inside micrometer. Available for all EMD Crankcases, one or two indicating heads can be snapped in place allowing the operator to locate the boring bar in a fraction of the time required with a micrometer. Once the boring process has begun, the indicating heads can be snapped in place for adjustments between cuts. These indicating heads are graduated in .0005” increments and have a full .120” of travel. A large heat-treated contact point reduces errors from pitting and metal transfer. Precision machined from aircraft aluminum, these Indicating Heads are lightweight and will last for years. |
|
|
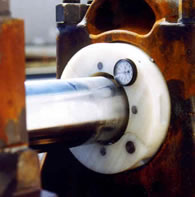 |
|
645 & 710 Roller Installation Tools |
Boring Bar Installation Tools are available for all EMD crankcases. These tools allow the operator to roll the boring bar in and out of the crankcase with minimal effort. During installation the Boring Bar Installation Tools locate the bar within .010” of the center of the bore, saving valuable time during the setup process. Precision machined to fit the crankcase, these tools utilize heat-treated bearings for years of reliable service. These tools are a must have for saving time and increasing efficiency. |
|
|
Image coming soon |
|
Carbide and Cermet Inserts |
Carbide inserts allow high speeds and long tool life while boring out EMD main bearing bores. These inserts are available in a variety of sizes and are tin coated for long life. Cermet Inserts are also available for those applications where the skim cutting is more frequent. Cermet inserts are designed for cuts less than .010” and provide excellent accuracy and repeatability. |
|
|
Image coming soon |
|
645 & 710 Digital Serration Gages w/ Master & Case |
Digital Serration Gages provide accurate measurements of main bearing cap and A-Frame serrations on all EMD Crankcases. These gages utilize digital technology and “go-no go” limits to provide your technician with fast and accurate readings. Precision machined from aircraft aluminum, these gages are lightweight and durable. Heat-treated steel contact points provide accuracy and repeatability.
All gages include Certified Serration Standards for setting the gage. SPC connections are available for your quality control purposes if needed. Both come in a high strength aluminum carrying case, keeping the gages clean and free from damage. |
|
|
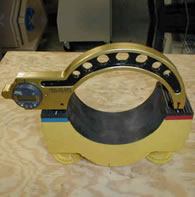 |
|
Clam Shell Extension Insert |
The Clam Shell Insert Bearing provides support for the “free end” of the boring bar. As the telescoping bar is extended, the natural frequency of the boring bar is lowered, slowing down the cutting speed of the machine. Inserting the Clam Shell Insert Bearing will support the free end of the bar, reducing vibration, allowing the operator to maintain high speed cutting. These Insert Bearings are manufactured from tough UHMW. They are lightweight and easy to use. Clamshell Insert Bearings provide the extra support needed particularly when machining 20 cylinder engines. |
|
|
Image coming soon |
|
60″ Boring Bar Standard |
Advanced Engineering provides precision ground Boring Bars available in 60” and 110” lengths. These bars are available for all of our boring machines. Each boring bar is heat-treated and chromed to last for years. Precision ground with .001 TIR, these bars look the same after years of service as the day they were new. |
|
|
Image coming soon |
|
110″ Boring Bar Upgrade |
Advanced Engineering provides precision ground Boring Bars available in 60” and 110” lengths. These bars are available for all of our boring machines. Each boring bar is heat-treated and chromed to last for years. Precision ground with .001 TIR, these bars look the same after years of service as the day they were new. |
|
|
Image coming soon |
|
Teflon Coated Adjustable High Speed Bearings |
Advanced Engineering Industries manufactures the best bearings in the business. Available for all EMD Crankcases, AEI applies a thin coating of Teflon to the ID of precision high-speed roller bearings. This combination allows the boring bar to be easily moved in the crankcase while providing roller bearing precision during cuts. Unlike the traditional brass or bronze bearing, our roller bearings create little heat, have lower clearance, and NEVER require lubrication. Heat-treated adjustment jackscrews provide years of service without rubbing the corners off the flats. |
|
|
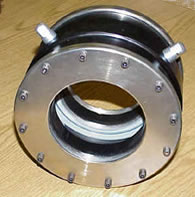 |
|
Teflon Coated End Mount Bearing |
Advanced Engineering Industries provides an additional bearing that mounts to the End Sheets of all EMD Crankcases. These bearings are laser cut from mild steel providing a lightweight bearing that has the rigidity for the application. Powerful magnets attach the bearing to the crankcase while setting up the boring bar. Teflon coated high speed roller bearings are used to provide an excellent surface finish and increased versatility when machining the
main bearing bores at the ends of the crankcase. |
|
|
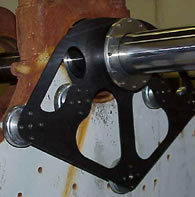 |
|
1″ – 2″ Starrett Inside Micrometer |
Coming soon |
|
|
Image coming soon |
|
Boring Bar Standards |
Boring Bar Standards are available for all EMD crankcases. These standards are solid steel and are heat-treated and ground for years of reliable service. These standards are available in a variety of sizes from 2.158”-2.661”. Adding these tools to your line boring process will increase the speed and accuracy of the procedure. |
|
|
Image coming soon |
|
|
|
» Contact Us |
Call us at 248-486-0354 to request a Product Catalog or Contact Us online today! |
|